How to Choose the Best Aluminum Cutting Machine
Have you ever encountered problems like burrs at both ends or uneven cuts when sawing aluminum pipes? Today, we will guide you to see the reason that causes these problems and find the best solutions to cut the aluminum pipes, aluminum tubes, aluminum profiles, and aluminum bars.
Why Burr Forms in Aluminum Profile Cutting?
When you cut aluminum profiles, aluminum pipes, or solid aluminum rods, sometimes the cuts will appear burrs or uneven. Do you know what’s the reason causes these problems?
Aluminum Cutting Machine Does Not Have Material Separation Function
The general aluminum cutting machine does not have the material separation function. When the saw blade retracts after cutting, it will drag on the cutting surface and then lead to burrs. However, if the aluminum cutting machine is equipped with a function that could automatically separate the cutting material after cutting, then such issues are avoided.
Saw Blade is Not Lubricate Inadequately
If it’s insufficient lubrication causing the issue with your saw blade, increase the lubrication amount. Then, start cutting again to see if the burr is due to insufficient lubrication.
Whether You Change to Different Material
Although you use an aluminum cutting machine specifically for cutting various aluminum profiles, there are numerous series of aluminum profiles, each with different characteristics. If you were originally cutting 5xxx series or 6xxx series aluminum profiles, and now you’re cutting 2xxx series or 3xxx series, the aluminum profiles are softer than before. So, you need to increase the lubrication oil quantity.”
Saw Blade Wear
Typically, a new saw blade needs regrinding or replacement after approximately 30,000 uses. When your cutting performance diminishes, check if your saw blade has worn out.
You may interested in our circular blade sharpener
The Saw Blade and the Flange were not Cleaned
When installing the saw blade and the flange, check for any aluminum chips on them and remove them promptly. Aluminum chips melted onto the flange can cause the saw blade to not clamp tightly, resulting in blade vibration and burrs during cutting.
The Saw Blade is not Compatible with the Material Being Cut
The saw blade has too few teeth, which can easily cause burrs during cutting. You need to choose the appropriate blade for the material you are cutting.
What is Aluminum Cutting Machine?
Aluminum cutting machine is an industrial equipment that is specifically designed to cut aluminum tubes, aluminum pipes, aluminum profiles, and aluminum bars. Common methods for cutting aluminum profiles include circular saw cutting, bandsaw cutting, CNC cutting, and laser cutting.
Types of Aluminum Cutting Machine
Before knowing which is the best aluminum cutting machine for your aluminum pipes or profiles, you need to know machine features, pros, and cons, so that you can decide which is the best aluminum cutting machine to meet your cutting needs.
Cold Saw
Cold saw is a type of circular saw that uses a circular saw blade to cut the material. This machine normally needs a coolant or lubricant to keep the blade and workpiece cooling during the cutting process. The cooling method helps to minimize heat generation, reduce friction, and extend the life of the saw blade.
Pros of Cold Saw
- High Precision: Cold saw provides accurate and precise cuts with clean and smooth cuts on the workpiece ends.
- Clean Cuts: Cold cut saw uses the coolant or lubricant to minimize the heat generation, and then leads to minimal burrs and material distortion.
- Versatility: The circular cold saw can cut on various metal materials, including steel, aluminum, stainless steel, and other alloys.
- Easy to Operate: The cold cut metal saw is very easy to operate, you don’t have to specially train operators. This is a machine that you can operate almost as soon as you get started.
- Low Maintenance: Very easy to maintain and only need saw blade sharpening. You don’t need to shut down for a long time, so the production efficiency is very high.
- Low Cost: Cold saw is normally affordable for most industries business.
Cons of Cold Saw
- Slower Cutting Speed: The cold metal saw normally has a slower cutting speed compared to other cutting methods.
- Noise: This machine can generate significant noise during cutting, so need you to equip workers with earplugs.
Bandsaw
Bandsaw is a power tool used for cutting various materials, including wood, metal, and plastic. It consists of a continuous band saw blade stretched by two or more rollers. Feed the material into a band saw and the blade rotates around the wheels to create a precise cut.
Pros of Bandsaw
- Versatility: Band saws can cut metal, wood, and plastic, so this machine can work for various applications.
- Efficiency: Bandsaws can cut a large amount of material which is a great feature to improve efficiency.
- Flexibility: Bandsaw can cut your materials into irregular shapes.
Cons of Bandsaw
- High Cost: It depends on how you use the bandsaw, and how frequently you use it. Especially if you are looking for a high-end model, the cost is high.
- Takes Up A Lot of Space: If you are looking for an industrial band saw, it usually requires a certain amount of space to work, this is not friendly to someone who only has limited space.
- Maintenance: The band saw needs you to change the bandsaw blades, adjust the tension, and also lubricate the mechanism.
- Noise: Band saws can be very noisy, which may require you to think carefully about where and when you use them.
Semi-automatic Aluminum Cutting Machine
Our semi-automatic aluminum cutting machine is specifically designed to cut aluminum profiles, tubes, pipes, and angles. This machine is not only suitable for cutting aluminum but also can cut copper, PVC, plastic steel materials, bakelite boards, acrylic plastic, Teflon, wooden boards, etc.
Pros of Semi-automatic Aluminum Cutting Machine
- Concealed blade, can operate safely up and down.
- Automatic oiling, burr-free cuts, longer-lasting saw blade.
- Multiple cuts at once, improving production efficiency.
- Can cut at 90 degrees/45 degrees angle.
- Addressing the issue of traditional machine’s aluminum chip splatter, improving the work environment.
- Adjustable working time and pressure.
- Cut thin-wall materials without deformation, fast speed.
Cons of Semi-automatic Aluminum Cutting Machine
- The cutting accuracy is not as high as fully automatic.
- Requires additional manpower costs.
Automatic CNC Aluminum Cutting Machine
The fully automatic CNC aluminum cutting machine is an advanced version of the semi-automatic, specialized for cutting various aluminum profiles with high precision and efficiency.
Pros of Automatic CNC Aluminum Cutting Machine
- Concealed blade, can operate safely up and down.
- Touch screen for setting length, adjustable feed length at any time.
- Automatic oiling, burr-free cuts, longer-lasting saw blade.
- Cut multiple pieces at once, enhancing production efficiency and reducing labor intensity.
- The material-sensing device can automatically stop the machine after the workpiece is processed.
Cons of Automatic CNC Aluminum Cutting Machine
- The cost of a fully automatic type is higher than the semi-auto. If you need to cut a large quantity of aluminum materials, this machine is highly suitable. However, if you only require a small amount of cutting, we recommend the semi-automatic option instead.
- You need more time and effort to train employees to operate automatic CNC aluminum cutting machine, or you need to spend more to hire a skilled worker.
Tube Laser Cutting Machine
The tube laser cutting machine is an industrial equipment that is specifically used for precisely cutting various tubes and profiles made from metal, including steel, stainless steel, aluminum, etc. You will have an extremely accurate and clean cut with better cutting performance by using a tube laser cutting machine since this equipment uses a high-powered laser beam to melt, burn, or vaporize the material along the programmed cutting path.
Pros of Tube Laser Cutting Machine
- High Accuracy: A tube laser cutting machine is a great choice for request that has complex cuts with tight tolerance.
- Clean Cuts: Cutting by tube laser cutting machine will have flat, smooth, and clean cutting edges with minimal distortion. You don’t need a secondary finishing operation due to the excellent cutting result.
- No-contact Cutting: Laser cutting is a non-contact process, which means there is no tool wear or physical contact with the workpiece, this cutting method almost does not have any material deformation.
- High Efficiency: The tube laser cutting machine is suitable for mass production.
- High Flexibility: The tube laser cutting machine can not only process straight cuts but also complex contours.
- Integration with CAD/CAM Software: The tube laser cutting machine can be seamlessly integrated with CAD and CAM software, so this machine is suitable for complex cutting.
Cons of Tube Laser Cutting Machine
- High Cost: Tube laser cutting is the most expensive investment among all the tube cutting methods, it is not suitable for small businesses.
- Maintenance Requirements: You need to regularly maintain the laser tube cutting machine, including alignment checks, lens cleaning, and replacement of consumable parts.
- Limited Thickness: This is dependent on different machine manufacturers, most laser tube cutting machines cutting depth is limited to 12mm. You need a larger power machine to cut thicker material.
- Complexity: Those who operate laser pipe-cutting machines require specialized knowledge, especially when it comes to programming, setup, and maintenance. This requires you to spend extra time and cost to obtain.
- Energy Consumption: Laser-cutting machines consume huge amounts of energy during operation, especially when cutting thicker materials or operating at high speeds.
Why Do We Need Dedicated Aluminum Cutting Machine?
The above machinery provides the most common cut aluminum pipe methods on the market. As you can see, Theoretically, they can all cut aluminum pipes, but some of them are high cost, and some of them do not have perfect cutting performance, this is why we need to recommend semi-automatic aluminum cutting machine and automatic CNC aluminum cutting machine to you – the best way to cut aluminum tubing, they are specifically designed for cutting aluminum tube with good performance and affordable cost.
Maybe someone will say, that the cold saw also can cut aluminum tubes, so why don’t you use it to cut aluminum tubes? Yes, the cold saw can cut aluminum pipe and profiles, but the cutting result is not good, they are always not smooth, especially if you are a factory and need to cut lots of aluminum tubes and profiles for your business. Let’s see why the dedicated aluminum cutting machine is better than cold saws.
- Compared to other metal tubes, aluminum tubes have a lower melting point and soften easily. This means that aluminum is more susceptible to heat when cutting and may have deformation or stickiness at the cut edge.
- The aluminum tube cutting machine is equipped with special lubrication systems and material handling capabilities, they can ensure the cutting edge without burrs.
- The equipment can extend the saw blade service life, and also the special saw blade for aluminum cutting can improve the cutting quality.
- After a period of bulk cutting with cold saw blades, aluminum tubes tend to develop burrs easily. Therefore, using an aluminum cutting machine for mass production can enhance your production efficiency, ensuring optimal cutting surfaces for every aluminum tube.
Applications of Aluminum Cutting Machine
As we all know, aluminum tubes and profiles can be used everywhere, this means the aluminum cutting machine is suitable for various industries, including furniture, outdoor, construction, automotive, aerospace, electronics, and manufacturing.
Key Considerations When Choosing the Aluminum Cutting Machine
After knowing which machinery type is the most suitable for cutting aluminum profiles, what do you need to consider before purchasing?
Aluminum Tube/Profile Size
Before purchasing the aluminum cutter machine, you need to know your material maximum size, then you can communicate with the aluminum tube cutting machine factories for their machine working capacity.
Cutting Accuracy
After knowing your product request on accuracy, you need to provide these parameters to the machine supplier to talk with them about whether their machine can meet your request.
Productivity
Check with your production department, what are their requirements on machine equipment’s productivity or ask them to customize machinery that meets your demands.
Operation and Maintenance
Among all the supplier who can meet your request, see if their equipment is easy to operate and maintain. This is related to whether it is conducive to later management after you purchase the equipment.
Machine Cost
After checking all the technical requirements with the supplier, choose those who can meet your requirements and compare their quotation to you.
Care Tips for Aluminum Cutting Machine
Knowing the care tips will benefit you in extending the machine’s service life, improving productivity, and improving cutting quality.
The Compatibility of Cutting Materials with Machines
Even within aluminum profiles, there are various types and grades. Each aluminum cutting machine is designed to accommodate specific materials. It’s essential not to exceed the machine’s compatibility range to avoid equipment damage, blade wear, and poor cutting results.
Always Keep the Aluminum Cutting Machine in Good Condition
If you notice any abnormalities during equipment operation, please stop immediately. Seek professional assistance to inspect the equipment and ensure that any issues are resolved before resuming cutting operations.
Regularly Lubricate and Maintain the Aluminum Cutting Machine
It’s essential to regularly maintain the aluminum cutting machine. This not only keeps the equipment in optimal working condition but also extends the lifespan of its transmission and other related components, reducing the risk of machine failure.
Schedule Maintenance Based on Machine Usage
Make a comprehensive maintenance schedule based on the frequency of use of the aluminum cutting machine. Regularly inspect the machine to ensure its functionality and check for any damages. These maintenance checks aim to ensure the machine operates properly and performs effectively for the next use.
TubeBenderN is one of the best aluminum cutting machine manufacturers in China, we produce both NC and CNC aluminum tube cutting machine with custom service. If you are looking for a specialized aluminum tube and profile cutting machine, contact us for the best solution!
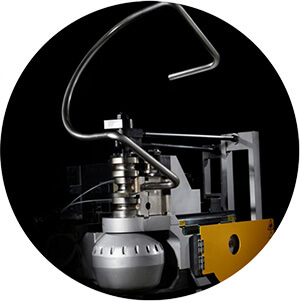
Denis Lau
Denis Lau has 20 years of work experience in the metal processing industry. His major in university was mechanical engineering, and after graduation, he started from the bottom of the workshop, gaining extensive hands-on professional experience and the ability to tackle challenges from various industries.