Exploring the Power of CNC Tube Punching Machine
- What is CNC Tube Punching Machine?
- What Makes CNC Tube Punching Machine Different from Other Tube Punching Method?
- The Application of CNC Tube Punching Machine
- The Benefits of CNC Tube Punching Machine
- Key Components of CNC Tube Punching Machine
- How the CNC Tube Punching Machine Works?
- Factors You Need to Consider Before Purchasing a CNC Tube Punching Machine
Tube punching plays an important role in a wide range of applications. Some manufacturing only requires punching a single hole, while others require many holes in accurate position at once. Sometimes it’s round holes, sometimes it’s square holes, and sometimes it’s various different shapes.
In the past, workers used manual punch machines or single punch presses to punch holes, but they could not meet the demand of the increasing market and rising customer expectations. Now, CNC tube punching machine can punch different shapes of holes at some time with precise positioning, improving the working efficiency and workpiece quality.
What is CNC Tube Punching Machine?
CNC tube punching machine is an advanced equipment designed to automate the hole punching process on tubes and pipes. This machine is controlled by CNC (computer numerical control) technology to precisely position the tube, and control the punching mechanism to achieve accurate and consistent hole patterns.
What Makes CNC Tube Punching Machine Different from Other Tube Punching Method?
Compared with the traditional tube punching method, CNC tube punching machines rely on computer programming and punch many holes in the tube simultaneously. Even if you want to punch multiple shapes of holes on a single tube, this machine also can be achieved by custom tube punching dies. Contact our engineer to custom CNC tube punching machine today!
The Application of CNC Tube Punching Machine
A lot of industries that use metal tubes require tube punching for some specific usage. Some of them can be proceeded by simple tube punching machine due to they only need 1-2 holes in the tube. But some other applications, they require multiple holes or perforations punched through their walls in a specific pattern. The CNC tube punching machine is designed to make such perforated metal tubes come true with high accuracy with high productivity.
Filtration Systems: Metal tubes used to make filtration systems need to punch many holes in one single tube. Such perforated metal tubes enable effective fluid or air filtration to pass through and capture impurities and particles.
HVAC Ductwork: Ventilation ducts require the CNC tube punching machine to punch the precise holes on the tube for efficient airflow and temperature control.
Automotive Exhaust Systems: The pipe used in the automotive exhaust system always needs to punch holes to allow the gas flow and emission.
Furniture Design: Producing metal furniture always needs the tube punching machine to make holes on it, for both functional and aesthetic purposes.
Architectural Railing and Balustrades: For some metal railings and balustrades, also need CNC punching for multiple holes on the tube to create artistic touch for buildings.
Manufacturing and Metal Fabrication: Metal processing factories process different types of metal parts. Owning a CNC tube punching machine will help you to improve the tube punching efficiency.
Aerospace Components: CNC tube punching is also used to punch holes for aerospace components.
The Benefits of CNC Tube Punching Machine
As you can see too many types of punching machines on the market, and why do we consider the CNC automatic tube punching machine to be the most suitable tube punching machine for industrial production? Let’s take a look at its benefits.
Precision and Consistency: CNC tube punching machine offer highly accurate hole sizes, accurate hole positioning, and highly accurate hole patterns consistently for various industries.
Time and Cost Savings: The CNC tube punching machine is automatic. With such machinery, the labor cost will be reduced and improve your productivity.
Versatility and Customization: This machine can process different types of metal tubes and different materials of metal tubes. You can custom punch a wide range of hole patterns by the machine.
Reduced Waste: Doesn’t like other tube punching machines, CNC tube punching can optimize the hole placement and reduce material wastage.
Enhanced Safety: Using the automatic CNC tube punching machine can not only greatly reduce human error, but also protect the worker to operate the machine directly.
Integration with CAD/CAM Software: CNC tube punching machines can seamlessly integrate with computer-aided design (CAD) and computer-aided manufacturing (CAM) software, simplifying the design-to-production workflow.
Key Components of CNC Tube Punching Machine
CNC tube punching machine is an industrial equipment that consists of many parts. Today, we will see the key components of this machine.
Tube Feeding System: After setting the parameters, the tube feeding system will feed the tube into the machine, ensuring the accurate position for tube punching.
Punching Head: The hole punching tool is installed on the punching head to process the hole punching. The punching head moves according to programmed coordinates to create holes in the tubes.
Clamping Mechanism: The function of the clamping mechanism is to fix the tube during the punching process, in order to avoid tube movement or misalignment.
Computer Numerical Control (CNC) System: The CNC system is like the brain of the machine, after the engineer has designed the programmed instructions, the system can control the movement of the punching head automatically.
CAD/CAM Software Interface: The CNC tube punching machine always integrates with CAD and CAM software, so users can design the hole patterns and generate the instructions.
Control Panel: The control panel is very friendly to users, operators can use this interface to set the machine’s operating parameters and monitor the machine’s operating status.
Safety Features: CNC tube punching is equipped with an emergency stop button, and interlocks to protect the operator. If you also need other types of safety features, you can custom from us.
How the CNC Tube Punching Machine Works?
Tube punching sizes, tube punching patterns, and machine capacity need to be customized according to specific cases, but the main working process of CNC tube punching machine is the same.
Tube Loading
First, the tube is securely clamped on the feeding system, make sure the tube can be firmly fixed on the machine.
CAD/CAM Design
The engineer uses the CAD software to create the hole pattern, hole size, and hole location for tubes, then the CAD software generates a digital design file that contains the coordinates for each hole.
CAM Programming
Import the CAD-designed file into CAM software, the CAM software generates the CNC program (G-code) based on the CAD design, giving instructions to the machine on how to move the punching head, and how to position the tube.
CNC Machine Setup
The operator loads the G-code into the CNC tube punching machine control system, once the punching die is installed on the machine, then ready for punching the customized hole patterns.
Automated Punching
Once everything is set up, the CNC tube punching machine starts to punch holes in tubes automatically. The control system coordinates the tube feeding system, tube punching head, and tube clamping mechanism, making sure that the hole punching on the tube completely fits the customer’s request.
Punching Process
Once the punching head with the punching tool is at the right position, it will move down with force rapidly to create holes that are exactly the same as the CAD design. This machine’s high speed allows it to punch efficient holes with high productivity.
Continuous Operation
If your customized hole patterns are all around the tube, once the punching head finishes one side of the tube, the clamping mechanism will rotate the tube and then the punching head will process its next instructions.
Factors You Need to Consider Before Purchasing a CNC Tube Punching Machine
Before purchasing a CNC tube punching machine, you need to know the specific tube parameters and some factors you need to consider.
Machine Size and Capacity Considerations
Know clearly about the tube size range you need to punch, especially the largest tubes so that you can confirm the machine’s working capacity to fit all your tubes.
Knowing specific tube sizes is also great for customizing different punching dies and other accessories for better punching results.
Knowing the size of the machinery in advance allows you to better plan the available area of the workshop. When the machine arrives at your factory, you can put it there.
Types of Hole Patterns and Tooling Options
You may have different patterns of holes on the tube, so design the shape, size, position, and spacing of the holes needed for each type of tube, you can customize the punching dies accordingly and achieve mass production accurately.
You can customize round holes, square holes, oval holes, or even punch multiple hole patterns on a single tube, all these you can achieve with our CNC tube hole punching machine. Contact our engineer to customize your machine Now!
Software and Programming Capabilities
The tube punching machine should be compatible with standard CAD/CAM software so that you can easily design your tube punching drawing and generate the code for the machine easily.
Maintenance and Support Services
Choose the machine that uses the world famous spare parts and quick-wear parts, so when they need to be replaced, you can easily find them in your local shop.
Choose the machine that is strong and does not need to be maintained frequently.
Choose the machine that is easy to operate.
If the machine you want to purchase is complex and always updated, you should find the one that is close to you and they can come to the site at any time to provide you with technical guidance.
Automation and Integration
Check the automation of your CNC tube punching machine, if the machine has advanced automation capability, your factory can greatly reduce the labor cost.
If you do not want any workers in the factory, check with the machine supplier, if this machine can integrate with the robot mechanical arm.
Cost and Return on Investment (ROI)
Compare the cost of CNC tube punching machine with other types of tube punching machine.
Assess return on investment based on increased productivity, reduced material wastage, reduced labor cost, etc.
Other Customized Options
Discuss with engineers about the customized options you want, such as the safety features of the machine, different language selections, etc.
At TubeBenderN, we are committed to staying ahead of providing state-of-the-art CNC tube punching solutions. Experience the efficiency, precision, and versatility of our machines to elevate your manufacturing processes. Contact us to get your tube punching solution Today!
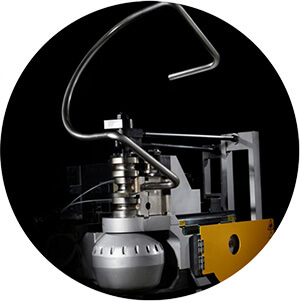
Denis Lau
Denis Lau has 20 years of work experience in the metal processing industry. His major in university was mechanical engineering, and after graduation, he started from the bottom of the workshop, gaining extensive hands-on professional experience and the ability to tackle challenges from various industries.