A Comprehensive Guide to Tube Cutting Machine
Whether you are a metal tube processing factory or a specialized product manufacturer, as long as your production involves metal products, you will need a tube cutting machine. Choosing a cost-effective, versatile tube cutting machine that fits your production needs is very important.
What is a Tube Cutting Machine?
A tube cutting machine is an industrial equipment that is used to precisely and efficiently cut various types of tubes and pipes.
For some industries that heavily rely on tubes and pipes, tube cutting machines will help them to improve their productivity and product quality. There are different types of pipe cutting machines that can offer different pipe cutting techniques, let’s take a look at them and see which is the best machine for your needs.
Types of Tube Cutting Machine
There are many tube cutting techniques in the market, such as laser cutting, plasma cutting, and abrasive waterjet cutting. Today, we’ll divide them into two categories: CNC tube cutting machine and mechanical tube cutting machine, and introduce them to everyone.
CNC Tube Cutting Machine
Equipped with the CNC control system on the tube cutter machine can achieve precise tube cutting with automatic cutting function, who are they?
Laser Tube Cutting Machine
A laser tube cutting machine uses a high-powered laser beam to melt, burn, or vaporize the material along the desired cutting path.
Applicable Cutting Materials
Metal, steel, aluminum, stainless steel, wood, copper and plastic.
Cutting Capacity of Laser Tube Cutting Machine
- Cutting Diameter: 10mm
- Cutting Diameter: 350mm
- Laser Power Supply: From 1000W to 6000W
- Chuck Speed: From 60r/min to 100r/min
- Chuck Air Pressure: 0.4-0.9Mpa
- Blanking Length: 25D
- Chuck Rotation Accuracy: ≤1mm
- Chuck Repeat Positioning Accuracy: ≤1mm
Cost of Laser Tube Cutting Machine
The price of laser tube cutting machines from different manufacturers is different, due to different materials, functions, working capabilities, and so on. Generally, the CNC laser tube cutting machine costs at least USD 14,000 per set.
Advantages
High Precision: Laser tube cutting performs high precision cutting results, without any burrs.
High Efficiency: Cutting speed is very quick and suitable for mass production.
Flexibility: Suitable for complex tube cutting, not only straight cutting but also angle cutting.
Non-contact Processing: There’s no part of the laser tube cutting machine that contacts the workpieces while working, so reduces the damage to it.
High Automation: This can be integrated with an automation system, achieving automatic manufacturing.
Disadvantage
High Cost: Both the purchasing cost and maintenance cost of the laser tube cutting machine are high.
Power Consumption: Operating laser pipe cutting machines normally consumes more power.
Cutting Thickness Limitation: Different laser tube cutting machines have different capacities, but most of them can cut the thickness Max. to 25mm.
High Requirements for Working Environment: Needs stable stable working environment, or else, the environment will affect the laser beam.
Plasma Tube Cutting Machine
Plasma tube cutting uses ionized gas (plasma) to cut metal tubes, an electric arc is formed between the plasma torch and the metal, melting the material and blowing away the molten metal. Plasma cutting is cut much quicker than other cutting methods and is very suitable for cutting thick material.
Applicable Cutting Materials
Conductive metals include: copper, brass, stainless steel, aluminum, carbon steel, and mild steel.
Cutting Capacity of Plasma Tube Cutting Machine
- Tube Diameter Range: From 25mm to 600mm
- Tube Length: Can be customized
- Cutting Mode: Plasma Cut
- Cutting Speed: 10-6000mm/min
- Moving Speed: 0-8000mm/min
- Working Precision: 0.1mm
- Working Temperature: -10℃ to 45℃
Cost of Plasma Tube Cutting Machine
Depending on different designs, and different working capacities, the price of plasma is different from different manufacturers. Generally, this machine costs at least USD5000 per set.
Advantages
High Speed Cutting: The plasma pipe cutting machine’s cutting speed is very quick and suitable for mass production and requires high efficiency.
Wide Cutting Size Range: Can cut thicker metal tubes.
Flexibility: Can cut different shapes of tubes, and meet different cutting requirements.
Disadvantages
High Cost: The purchasing cost and maintenance costs of the plasma tube cutter are very high.
Lower Cutting Edge Quality: Compared with the laser tube cutting machine, the cutting edge of the plasma pipe cutting machine is rough.
Workpiece May Be Deformed: Due to the HAZ, some tube materials may deform.
Abrasive Waterjet Tube Cutting Machine
An abrasive waterjet tube cutting machine uses a high-pressure jet of water mixed with abrasive particles to erode the material, resulting in precise cuts.
Applicable Cutting Materials
All metals, including: steel, stainless steel, aluminum, titanium, brass, copper, etc. Non-metals, including: glass, ceramics, composites, plastics, rubber, foam, etc.
Cutting Capacity of Abrasive Waterjet Tube Cutting Machine
- Effective Distance of X Axis: From 1000mm to 3000mm
- Effective Distance of Y Axis: From 2000mm to 6000mm
- Effective Distance of Z Axis: 120/150mm
- Pressure: From 300MPA to 420MPA
- Water Flow: 3.7L/min
- Running Speed: 9000mm/min
- Cutting Accuracy: ±1mm
- Control Accuracy: ±01mm
- Repeat Accuracy: ±05mm
Cost of Abrasive Waterjet Tube Cutting Machine
Due to different design, different function, different working capacity of the machine, the price will vary. Generally, the abrasive waterjet tube cutting machine costs at least USD4500-5000 per set.
Advantages
High Precision: Cutting by abrasive waterjet tube cutting machine will have high cutting precision, tolerance is +/-0.001’’.
Cold Processing: No heat affected zone and avoid material deformation.
No Pre-Processing Required: No special tooling to fix the workpiece, and simplify the preparation.
Wide Processing Range: An abrasive waterjet tube cutting machine can cut both metallic and non-metallic materials.
Eco-Friendly: No need to use chemicals or coolants to avoid pollution to the environment.
Disadvantage
Slower Cutting Speed: Compared to other cutting methods, waterjet cutting speed is relatively slow.
High Energy Consumption: Need lots of water and energy to create the high pressure waterjet.
Need to Replace Abrasive Regularly: The maintenance cost increased because the abrasive wears down with use and you need to replace it regularly.
Limited Cutting Thickness: For thicker metal material, you will need more energy and a long time to process. Remember, the thicker the material, the lower the precision of waterjet cutting.
Automatic Cold Saw
An automatic cold saw is an automatic tube cutting machine that uses a circular saw blade to cut metal tubes and profiles. The machine is integrated with the CNC system to allow the cutting process automatically. This is a dedicated machine for the metalworking and fabrication industries.
Applicable Cutting Materials
Carbon steel, mild steel, iron, stainless steel, aluminum, copper, brass, etc.
Cutting Capacity of Automatic Cold Saw
- Cutting Capacity: φ60mm
- Feeding Length: Can be customized
- Driven Mode: Can customize hydraulic or servo motor
- Cutting Accuracy: ±1mm
- Saw Blade Rotation Speed: 60/120RPM, 18/36RPM
- Working Pressure: 70kg
- Size and Weight: Depend on different manufacturers.
Cost of Automatic Cold Saw
Due to different configurations of automatic cod saws, the price of this machine from different manufacturers is different. Generally, this type of machine costs at least USD6000 per set.
Advantages
High Precision: CNC cold saw can cut the material with high precision without burrs.
High Efficiency: Improve productivity by automatic operation and fast cutting speed.
Better Cutting Ends: Cold cutting techniques make the tube cutting ends smoother, with no more subsequent processing.
Wide Applicability: Not only suitable for tubes and pipes but also suitable for cutting metal profiles and solid bars.
Disadvantage
High Initial Cost: The purchasing cost is relatively high.
Maintenance Cost: Need to replace the saw blade and cut lubricate when needed.
Flexibility: For cutting the large diameter workpiece and irregular workpiece, the flexibility of the automatic cold saw may not be as good as others.
Automatic Band Saw
The automatic band saw is also a type of cutting machine that is equipped with a band saw, this machine is integrated with a CNC system to achieve automatic material feeding and cutting.
Applicable Cutting Materials
The band saw can cut various materials, like steel, aluminum, brass, copper, alloys, acrylic, polycarbonate, lumber, plywood, fiberglass, carbon fiber, natural rubber, polyurethane foam, polystyrene foam, etc.
Cutting Capacity of Automatic Band Saw
- Cutting Diameter/Size: 800mm
- Blade Speed: 27/45/69 m/min
- Blade Size: 8377*54*1.6mm
- Main Transmission Structure: Worm Gear Transmission
- Main Motor: 7.5kw
- Hydraulic Motor: 3kw
- Single Feed Length: 500mm
- Feeding Precision: ±2mm
- Size and Weight: Based on different manufacturer
Cost of Automatic Band Saw
Due to the different configurations of the automatic band saw from different manufacturers, the price of this machine is different. Generally, the cost of automatic band saw will cost at least USD2500 per set.
Advantages
High Efficiency: Automatic feeding and cutting can achieve continuous production and high productivity.
High Precision: Due to CNC control, cutting results will be consistent with high precision.
Versatility: Suitable for cutting a wide range of products, including metal, rubber, wood, etc.
Disadvantages
High Initial Cost: The purchasing cost of an automatic band saw is high.
Complex Maintenance: Need expert and technical to maintain the complex equipment.
Cutting Size Limitation: Due to the size limitation of the band saw, the machine’s cutting capacity is also limited.
Potential Safety Hazard: Operating the automatic band saw requires certain skills, improper operation may result in accidents.
Mechanical Tube Cutting Machine
For smaller factories with less tube cutting demands or the one do not have high precision and efficiency, mechanical tube cutting machines are enough for them to meet production requests.
Manual Band Saw
A manual band saw is a band saw that needs to be operated by a human, such as feeding the material, adjusting the cutting length, cutting quantity, cutting speed, etc.
The applicable cutting materials of a manual band saw should be the same as the CNC band saw, but pay attention to different machine capacities.
Cutting Capacity of Manual Band Saw
- Cutting Size: 330mm (Max.)
- Cutting Angle: 45°,90°
- Return: Manual
- Size and Weight: Based on different configurations from different manufacturers
Cost of Manual Band Saw
Manual band saw from different manufacturers will have different configurations, so the price is different. Generally, the manual band saw will cost at least USD150 per set.
Advantages
Portability: Generally, the manual band saw is lighter and easy to move to any job site you want.
Easy to Use: No need for programming, easy to operate.
Low Cost: The purchasing cost is much lower than the automatic band saw.
Disadvantages
Low Efficiency: Manual operation leads to lower efficiency, not suitable for mass production.
High Labor Cost: Manual operation needs more labor cost and misoperation.
Limited Cutting Accuracy: Compared with the CNC type, the cutting accuracy of the manual type is lower.
Limited Cutting Size: Can not proceed with complex cutting tasks and large workpieces.
Manual Cold Saw
A manual cold saw is a circular saw machine that operates manually, mainly used to cut metal workpieces. Manual cold saws are suitable for small scale production that does not require high productivity.
Applicable Cutting Materials
Used to cut tubes in these materials: steel, aluminum, stainless steel, brass, copper, bronze, alloy steel, etc.
Cutting Capacity of Manual Cold Saw
- Cutting Diameter: φ100mm
- Blade Rotation Speed: 60/120RPM
- Angle Adjustment Range: ±45°
- Compressed Air: 6-8kg/ c㎡
- Machine Weight: 250kg
- Machine Size: 1.1m³
Cost of Manual Cold Saw
The same, due to different configurations of the manual cold saw from different manufacturers, the price is different. Generally, the manual cold saw costs at least USD1000 per set.
Advantages
Versatility: Can cut both ferrous and non-ferrous metals.
Cost Effective: A manual cold saw is more affordable than a CNC cold saw.
Precise Cut: Relatively have precise cut by manual cold saw, if the worker is well trained, the saw blade is of high quality.
Easy to Operation: This manual type is easy to use, even if you do not have professional training.
Disadvantages
High Labor Cost and Low Efficiency: Manual operation needs workers and needs to be trained regularly. This machine also does not have high productivity.
Cutting Quality Varies: Tube cutting quality varies due to different operators, making the cutting quality inconsistent.
Limited Cutting Capacity: A manual type cutting machine only can cut simple tubes with limited size.
Pneumatic Cold Saw
A pneumatic cold saw is a tube cutting machine that relies on compressed air to power its cutting action.
Applicable Cutting Materials
Used to cut tubes in these materials: steel, aluminum, stainless steel, brass, copper, bronze, alloy steel, etc.
Cutting Capacity of Pneumatic Cold Saw
- Cutting Diameter: φ95mm
- Saw Blade Rotation Speed: 60/120RPM
- Compressed Air: 6-8kg/cm
- Machine Weight: 280kg
- Machine Size: 1.1m³
Cost of Pneumatic Cold Saw
Depend on different configurations of pneumatic cold saw from different manufacturers, the price will vary. Generally, this type of machine costs at least USD1300 per set.
Advantages
Cutting Speed: A pneumatic cold saw has a faster cutting speed than a manual cold saw.
Accuracy: Cutting accuracy is higher than manual type, tube cutting edge is smooth.
Versatility: Can cut both ferrous and non-ferrous metals.
Cutting Capacity: Can cut larger tube sizes than the manual type.
Disadvantages
Air Supply Dependency: A pneumatic cold saw requires your factory must have an air compressor to supply air.
Maintenance Cost: The pneumatic type requires you to have a stable air supply and pressure, this will increase your maintenance cost.
Hydraulic Cold Saw
A hydraulic cold saw is a pipe cutting machine that uses hydraulic power to drive the saw blade to process the cutting for tubes, pipes, and profiles.
Applicable Cutting Materials
Used to cut steel, aluminum, stainless steel, brass, copper, bronze, alloy steel, tubes, pipes, profiles, and solid bars.
Cutting Capacity of Hydraulic Cold Saw
- Cutting Diameter: φ140mm
- Blade Rotation Speed: 50/100RPM
- Angle Adjustment Range: ±45°
- Working Pressure: 70MPa
- Machine Weight: 650kg
- Machine Size: 1.8m³
Cost of Hydraulic Cold Saw
Based on different configurations of this machine from different manufacturers, the price will vary according to their actual cost. Generally, the hydraulic cold saw costs at least USD6000 per set.
Advantages
High Efficiency: With a powerful hydraulic system, this machine can cut pipes with high speed and high precision.
High Accuracy: Cutting with hydraulic cold saw can provide lower cutting tolerance than the pneumatic type, the cutting edge is very smooth.
Versatility: This machine can cut metal tubes, pipes, profiles, and solid bars.
Durability: The design of the hydraulic cold saw is strong and can cut the larger size of tubes than the pneumatic type.
Disadvantages
High Initial Cost: The purchasing cost of hydraulic cold saws is more expensive than any other mechanical tube cutting machine.
Maintenance Cost: You need to maintain the hydraulic system regularly, so it will increase the maintenance cost.
High Energy Consumption: This machine needs a high power hydraulic system to operate, which will lead to high energy consumption.
What Factors You Need to Consider When Choosing A Tube Cutting Machine?
Different applications will have different requests for tube cutting, so what factors do you need to consider before purchasing tube cutting machines? Let us have a look.
Tube Material
Different cutting pipe machines are suitable for cutting different materials. For example, a laser tube cutting machine can cut metals, and plastics, while a waterjet cutting machine is suitable for a wider range of materials, including non-conductive and heat-sensitive ones. Choose the machine that fits your tube material.
Tube Size
Check the working capacity of the pipe cutter machine, check your commonly used and frequently used tube size, and see if the machine capacity can cover your tube size. You can also consider if you need to use the machine to cut more size in the future.
Cutting Speed and Performance
This feature is related to your productivity and cutting performance needs. Check if the machine’s cutting speed can meet your request for productivity. Also, not all the machine’s cutting performance is very smooth, so you should integrate your cutting request with the machine’s performance and see which is the suitable machine for you.
Automation and Software Integration
Check if your production requires automatic tube cutting. If not, you can choose the mechanical tube cutting machine. If yes, you can choose one of the CNC tube cutting machines, check their features, and see which is the best fit machine for you.
Maintenance and Support
First, check if the manufacturer can provide reliable technical support. Second, purchase a machine that is solid, strong, and stable, and requires as little after-sales service as possible.
Consider all factors to determine which type of tube cutting machine is most suitable for your needs. You can also ask our engineer to find the best tube cutting solution for you.
Customization Options for Tube Cutting Machines
Tube cutting machine is a type of highly customizable equipment for tube fabrication factory. Based on different cutting requests, you can choose different machine models and machine types. Besides these, you can also customize other functions you want.
Emergency Stop Button: The machine should be equipped with the emergency stop button, it can be a foot pedal emergency stop switch or an emergency stop button by hand. This could allow the workers to stop the machine if any emergency happens.
Protective Enclosures and Barriers: You can customize the protective enclosures or barriers at the cutting head to prevent the workers from direct contact with the cutting area. When the cutting head is open, the cutting head should stop working.
Safety Sensors: Safety sensors are necessary when obstacles or interference are detected at the working area, the sensors can trigger machine shutdowns.
Laser Safety Measures: If the machine uses laser cutting technology, implement laser safety measures, such as interlock systems, warning signs, and protective eyewear, to safeguard operators from potential laser hazards.
Ventilation and Fume Extraction: If you are using plasma cutting, ventilation and fume extraction systems are necessary, the system will help to remove smoke and harmful particles and provide a healthy and safe working environment to the workers.
The Application of Tube Cutting Machine
Tubing cutting machine is a versatile equipment with various applications, after studying the above information, you will know clearly which is the suitable machine for you, or you can ask our engineer to provide the best solution for you. Let us have a look at the application that relies on the tube cut machine.
Automotive Industries
Tube cutting machines provide precise cuts to the automotive industry, such as making exhaust systems, roll cages, and chassis components.
Aerospace and Aviation
The aerospace and aviation industry has high standards for tube cutting requests, this application needs super high precision, and great cutting performance to make intricate components for aircraft structures.
HVAC Systems
Heating, ventilation, and air conditioning (HVAC) systems need a proper pipe cutting machine to make precise dimensions, so the HVAC manufacturer can make good quality ducts and pipes for efficient airflow and temperature control.
Furniture Manufacturing
Furniture manufacturer heavily relies on tube cutting machine, especially metal furniture manufacturers and furniture manufacturers with tubular frames. Great tube cutting performance will help them to make durable furniture.
Construction and Architecture
For cutting structural steel, handrails, and supports, a pipe cutting machine is also indispensable equipment for the construction industry. Cutting the pipe to a specific size to meet engineering specifications is the standard when you look for a proper cutting machine.
FAQs about Tube Cutting Machine
Q: Can tube cutting machines handle complex shapes and designs?
A: The tube cutting machine that integrates with the CAD and CAM software can execute the complex shapes and designs by programming the machine.
Q: What maintenance you should do for the pipe cutting machine?
A: Regular maintenance for the machine is necessary to make it work smoothly, the maintenance should include:
- Lubrication: Always check and maintain the machine’s moving part well-lubricated, in order to reduce friction and wear.
- Cleaning: Regular cleaning of the machine head, cutting parts, and other parts of the machine to prevent debris buildup.
- Calibration: Regularly calibrate the machine to ensure precise cutting accuracy.
- Cutting Tool Replacement: Replace cutting tools (e.g., laser lens, plasma nozzle, circular saw blade) when worn out to maintain cut quality.
- Inspection: Regularly inspect safety features, sensors, and critical components to identify and find issues promptly.
TubeBenderN is a professional manufacturer of CNC tube cutting machine and mechanical tube cutting machine in China, providing service to thousands of applications. Get in touch with us today to get your best tube cutting solutions!
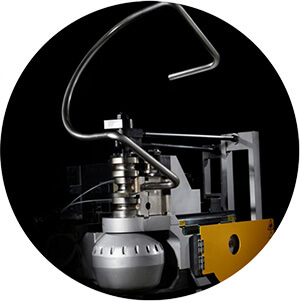
Denis Lau
Denis Lau has 20 years of work experience in the metal processing industry. His major in university was mechanical engineering, and after graduation, he started from the bottom of the workshop, gaining extensive hands-on professional experience and the ability to tackle challenges from various industries.