Difference Between Tube and Pipe
In real life, most people confuse the concepts of pipes and tubes, thinking that they are the same, just with different names, so they don’t distinguish them in life. Today, let’s take a look at the difference between pipes and tubes! If you often deal with pipes and tubes in your work, you will definitely benefit from this article.
What is Pipe?
A pipe is a large diameter, thick wall hollow cylinder, made of metal, plastic, or other materials. The pipe is primarily used to convey fluids (liquids or gases) or for structural applications.
What is a Tube?
A tube is a small diameter, thin wall hollow cylinder, that can be distinguished from a pipe by its intended use, which can include structural applications, heat exchange systems, and mechanical components.
Differences in Sizes
- Pipe: Large diameter, thick wall hollow cylinder.
- Tube: Small diameter, thin wall hollow cylinder.
Differences in Usages
- Pipe: Typically used to transport fluids and gases.
- Tube: Used in structural applications and for mechanical purposes.
Differences in Measurements
- Pipe: Measured by nominal size (NPS) and schedule (ID and wall thickness).
- Tube: Measured by outside diameter (OD) and wall thickness.
Differences in Tolerance and Precision
- Pipe: Generally, less stringent tolerances compared to tubes.
- Tube: Higher precision in measurements and tolerances, essential for their specific applications.
The Two Types of Tubing
Based on the different production processes, pipes can be divided into two categories: seamless tube and welded tube.
Seamless Tube
A seamless tube is manufactured from a solid cylindrical, called a billet. The billet is heated and then stretched over a series of mandrels to form a hollow tube.
- Strength: Stronger and more durable than welded tube.
- Applications: Often used in high-pressure applications, critical industrial components, the oil and gas industry, chemical plants, and automotive sectors.
Welded Tube
A welded tube is made by rolling a flat steel plate or strip into a cylindrical shape and then welding the seam to form a tube.
- Strength: The strength is lower than the seamless tube, especially at the welding point. The strength of welded tubes can be different based on different welding techniques.
- Applications: Commonly used in structural applications, construction, water and gas pipelines, automotive exhaust systems, and furniture manufacturing.
The Advantages of Seamless Tube
- Uniform strength around the circumference.
- Better resistance to corrosion and mechanical stress.
- Higher precision and quality in terms of dimensional tolerances.
The Disadvantages of Seamless Tube
- Complex manufacturing processes determine the higher cost.
- Limited in size compared to welded tube.
The Advantages of Welded Tube
- More cost-effective compared to seamless tubes.
- Available in larger sizes.
- Versatile in terms of material and application.
The Disadvantages of Welded Tube
- The welding seam can be a weak point under high pressure or stress.
- Poor mechanical properties compared to seamless tubes.
- During the production process, welding-related defects are prone to occur.
Shapes of Tubes
Tubes can be made into various shapes, here let’s take a look at 5 common types of tubes on the market.
- Round Tube: Round tubes are the most common shapes, generally used in plumbing, HVAC systems, automotive industries, structural applications, and more.
- Square Tube: Square tube means the tube cross-section is like a square, 4 sides are in the same length. Square tube is widely used in construction, fabrication, machinery, and structural applications.
- Rectangular Tube: The cross-section of the tube looks like a rectangular called rectangular tube. This tube shape is used in structural and architectural applications, construction, automotive frameworks, and furniture manufacturing.
- Oval Tube: The oval tube has an elliptical cross-section, often used in automotive exhaust systems, decorative applications, and furniture.
- Triangular Tube: A triangular tube has a triangular cross-section with three sides. This shape is less common but used in certain architectural designs, bike frames, and specialized machinery.
You should pay attention when you purchase the tube or pipe from your supplier, or even the related product, such as tube bender, because different measurement standards can cause ambiguity. For example, 1-1/4” tubing is not the same as NPS 1-1/4 pipe. For 1-1/4” tubing, the exact OD is 1.25’’. But for the NPS 1-1/4 pipe, the exact OD is 1.66’’.
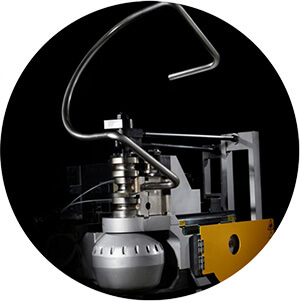
Denis Lau
Denis Lau has 20 years of work experience in the metal processing industry. His major in university was mechanical engineering, and after graduation, he started from the bottom of the workshop, gaining extensive hands-on professional experience and the ability to tackle challenges from various industries.