Which Tube End Forming Machine is Best
Tube end forming technology is highly important and widely applied in modern industrial society. A straight metal tube often cannot be used directly; it needs some forming processes on its surface or ends to better fit practical applications. Generally, we perform end forming on metal tubes for the following purposes:
- Enhance the connection and sealing performance.
- Realize customized connections.
- Enhance structural strength.
- Provide an attractive and consistent appearance.
So, which industry do you work in? Ok, come on, whatever industry you work for, you will find the best tube end forming machine that fits your production needs at TubeBenderN. Let’s start Now!
Tube Notcher
Tube notcher is one of the versatile tube forming machines that are used to notch holes in different angles and shapes on the tube. These notches can be made on both ends of the tube or the middle of the tube and then these parts can precisely connect to other tubes or fittings.
Tube notching machines can process on various metal tubes, such as carbon steel, stainless steel, copper, brass, aluminum, iron, etc., and no restriction on the shape of the metal tube, whether you use a round tube, square tube, or rectangular tube.
How to Use the Pipe Notching Machine?
- Fix the tube on the tube notching machine’s workbench.
- According to technical requirements, adjust the notching angle and position on the workbench.
- Start the machine, the chisel or cutting tool will move forward and cut the surface of the tube until the desired hole is notched.
- After notching, remove the tube from the machine and check the size and shape of the hole. If they meet the requirements of the drawing or technical specifications, then you can start mass production.
The Main Feature of Tube Notching Machine
- Cut Tooling: Used to cut the required notches or holes in the tube.
- Cutting Head and Bracket: The cutting head is usually adjustable to achieve cutting at different angles and shapes. The bracket ensures the stability and precision of the cutting tool.
- Hydraulic System: Provides the necessary power and speed control for cutting.
Technical Parameters of Tube Notching Machine
Whether which industry you are working for, when you are looking for the tube notcher, the working capacity of this machine must fit the needs of your production. Here are the basic technical parameters of this machine.
- Punching Size: φ80mm
- Punching Thickness: 2mm
- Adjustable Angle: 20° to 90°
- Motor Power: 7.5kw
- System Pressure: 14Mpa
- Machine Weight and Size: Based on different manufacturers
The Price of Tube Pipe Notcher
The price of pipe notchers from different manufacturers is different since their structure and configuration are different. Generally, the price of a pipe notching machine will cost at least USD 5,000 per set.
Application of Tube Notching Machine
- Automotive Industry: Tube notching machine is used to make the exhaust system, chassis support frame, and roll cage for the vehicle.
- Aerospace: Used to make aircraft and rocket frames, supports, and piping systems.
- Motorcycle Manufacturing: Used to make an exhaust system, chassis support frame, and bumper.
- Bicycle Manufacturing: Used to make frame, seat bracket, and handlebar bracket.
- Shipbuilding: Used to make hull structures, piping, and fittings.
- Building Structure Field: Used to make steel structures, stair handrails, and railings.
And more
In general, tube notchers are used to create holes of various shapes, sizes, and angles for precise pipe connections and assembly. They are not only easy to use but also can help you increase the production capacity.
You may also interested in:
The benefits of tube notcher in metal fabrication
To customize a tube notching machine that fits your production needs, contact our engineer to get your ideal machine.
Tube Flattening Machine
Tube end flattening machine is designed to flatten the ends or local areas of the tube into a flat shape, which is used to manufacture tube components that require specific shapes and connection methods.
People normally use the tube flattening machine to process round tubes, but this machine can also flatten square tubes and rectangular tubes in various materials, such as iron, carbon steel, stainless steel, aluminum, copper, and so on.
How the Tube Flattening Machine Works?
- Adjust the mold and parameters of the machine.
- Put one end of the tube into the clamping tooling and tube flattening die, and fix its position.
- Start the machine and gradually apply pressure to flatten the tube with a hydraulic system.
- Finally, check whether the flattened tube meets the request of drawing or technical requirements.
The Main Features of Tube Flattening Machine
- Workbench and Tube Clamping Tool: Used to position and fix the tube, and maintain the stability during punching process.
- Tube Flattening Tool (Die): Adjustable tooling, used to accommodate tubes in different sizes and shapes.
- Hydraulic System: Supply the power to apply the pressure to achieve flattening of the tube ends.
- Control System: Used to set and adjust the flattening parameters, and ensure the consistency of your mass production.
Technical Parameters of Tube Flattening Machine
This machine is high customizable, it is based on your specific tube size and needs. Here are the common parameters of this machine.
- Punching Size: 100mm
- Motor Power: 4kw
- Machine Weight and Size: Based on different manufacturers
Price of Tube Flattening Machine
Due to this machine needs to be customized according to your tube size and your production needs, so whether the machine configuration or the mold, many factors can affect the cost. Generally, the price of tube flattening machine will cost at least USD800 per set.
Application of Tube Flattening Machine
- Automotive Industry: Some chassis structural parts require flattening of tube ends for easier welding and joining.
- Building Structure: Used to make connection components in building steel structures to ensure stability and strength.
- Furniture Manufacturing: Used to manufacture leg connectors for tables and chairs, and support parts for bed frames, ensuring stable assembly.
- Consumer Electronics and Home Appliance Manufacturing: Used to manufacture the internal frames of household appliances, support frames, and fixing frames for electronic equipment, and provide strong connections.
Tube Expander & Tube Reducer
Tube expanding machine & tube reducing machine are the most common tube end forming machines used to expand or reduce the tube diameter according to request, tube expansion and tube reduction can be achieved on the same machine, only need to change to different tube forming die.
The tube expander and tube reducer are versatile and can be processed on different tube materials, such as iron tube, steel tube, stainless steel tube, copper tube, aluminum tube, etc. The machine can not only reduce/expand round tubes, and square tubes, but also can form the round tube into square tubes, or form the square tube into round tubes.
How does the Tube Expanding Machine/Tube Reducing Machine Work?
- Setting the tube reducing/tube expanding parameter.
- Fixing the tube into the clamping die.
- Start the machine and the tube expanding die/tube reducing die will move forward into the tube and gradually expand/reduce the tube diameter.
- After forming, check the size and shape. If this tube does not meet the customer’s request, you need to adjust the tube forming parameters
The Main Features of Tube Expander/Tube Reducer
- Clamping Die: Needs to be customized according to different tube sizes and shapes.
- Forming Die: This also needs to be customized according to the size and shape you want to form.
- Machine Working Station: If the size difference is large between the original tube and the expanded/reduced tube, you may need multiple working stations. Want to know which type of tube end formers fit your needs? Contact our engineer.
- Hydraulic System: Provide power for high-precision tube expansion and reduction.
- Control System: Adjust and control the parameters of the tube expansion/reduction process, such as pressure, speed, and time.
Technical Parameters of Tube Expander & Tube Reducer
The tube expander and tube reducer we talked about here do not mean the tools, we are talking about the industrial equipment that can be used for mass production. This machine is also highly customizable, so you’d better check with our engineer about your detailed request. Below are the basic technical parameters of this machine type
- Forming Tube Size: φ100mm
- Tube Diameter: 2.5mm
- Generally Forming Length: 210mm
- Pressure: 14Mpa
- Machine Size and Weight: Based on different manufacturers, this data may vary.
Price of Tube Expander & Tube Reducer
Due to this machine is customized according to specific tube size and tube shape, so the price of this machine is different. Some shape only need one time forming, but some other shapes need to shape multiple times, so this makes the machine configuration different. Generally, the tube expanding machine/tube end reducing machine costs at least USD4000 per set.
The Application of Tube Expander & Tube Reducer
- Boiler Manufacturing and Repair: Expand the diameter of boiler pipes to achieve tight connections and seals.
- Heat Exchanger Manufacturing: Expand the diameter of the heat exchanger pipe to improve heat transfer efficiency.
- Air Conditioning System Installation: Expanding pipes in air conditioning systems for precise fit and connection.
- Metal Processing: Metal processing companies usually need tube expanding machine and tube reducing machine to process different sizes and materials of tubes.
- Hydraulic System Manufacturing: Reduce the diameter of hydraulic pipes to achieve precise connections and fits.
- Fuel Line Installation: Reduce the diameter of the fuel line to ensure tight connection and sealing of the pipeline.
- Refrigeration System Manufacturing: Reduce the diameter of pipes in refrigeration systems, improving system efficiency and performance.
- Furniture Manufacturing: Form the round tube into the square tube, or form the square tube into the round tube to meet specific furniture design needs.
You may also interested in:
Tube Beading Machine
Tube beading machine also belongs to one type of tube end formers, used to form a convex or beaded structure on the end of a tube. The purpose of tube beading is to enhance the strength of the tube end, prevent the tube from slipping, and provide a contact surface for a sealed connection at the end of the tube.
The design of the tube beading machine is very similar to the tube expanding/reducing machine, the main difference is the tube beading die, and depending on the tube beading technical request, you may need single station or multiple stations tube end formers.
How the Tube Beading Machine Works?
- Setting the tube forming parameter in the microcomputer.
- Clamp the tube into the clamping tooling.
- Install the tube beading/forming die.
- Align the center of the round tube with the center of the forming die.
- Start the machine to form the beading on the tube.
- After finishing, measure the size and see if the formed tube meets the request.
The Main Features of Tube Beading Machine
- Clamping Tool: This needs to be made based on the size and shape of the tube that needs to be formed.
- Beading/Forming Die: Designed according to the customer’s request and use this forming die to form the final tube shape.
- Driving System: Generally, use the hydraulic system to supply the power and control the speed.
Technical Parameters of Tube Beading Machine
The tube beading machine is also one type of tube end forming machine, you can share the same machine with tube expander/reducer, just change the forming die according to the forming shape, if the working tube size is the same.
- Forming Tube Size: φ100mm
- Tube Diameter: 2.5mm
- Generally Forming Length: 210mm
- Pressure: 14Mpa
- Machine Size and Weight: Based on different manufacturers, this data may vary.
Price of Tube Beading Machine
As we mentioned above, tube beading can be processed on the same machine as tube expanding or reducing, you only need to change the forming die that fit for tube beading. So, if your factory tends to operate metalworking business, our tube end forming machine is your great choice. Generally, the tube beading machine costs at least USD4000 per set.
The Application of Tube Beading Machine
- Cooling System: A beaded structure is formed at the end of the cooling tube to provide better sealing and connection.
- Hydraulic System: A bead structure is formed at the end of the hydraulic pipe to ensure the sealing and connection of high-pressure liquid.
- Fuel System: Beads are formed at the ends of fuel lines to prevent fuel leaks.
- Washing Machines and Dishwashers: Beading is formed at the end of the drain pipe to increase the strength of the connection.
- Gas Delivery System: Forms a bead-like structure at the end of the gas pipeline to prevent gas leakage.
Tube Flaring Machine
Tube flaring machine is a kind is a tube forming machinery, used to form a flared shape on the end of the tube. This flaring helps to connect the pipes and joints, providing better sealing and stronger connection strength.
Tube flaring machine can form different sizes of metal tubes with different materials, such as copper tubes, aluminum tubes, steel tubes, stainless steel tubes, etc. You can customize the machine’s capacity to match your production needs. Unlike the general tube flare tool which is operated manually, it has limitations on the processing tube size, tube accuracy, and working efficiency.
How the Tube Flaring Machine Works?
- Setting the tube flaring parameters in the microcomputer.
- Install the tube flaring mold in the machine.
- Clamp the tube into the clamping tool.
- Align the center of the tube with the center of the mold.
- Start the machine to process the tube forming.
- Remove the tube from the machine and measure the size.
The Main Features of Tube Flaring Machine
- Tube Flaring Mold: This is customized according to the tube flaring shape and size of your customer.
- Driving System: Generally, the machine is driven by the hydraulic system.
- Clamping Tool: This needs to be customized according to your tube size.
Technical Parameters of Tube Flaring Machine
Tube flaring can be processed on the same tube end forming machine as tube expanding, tube reducing, and tube beading. You only need to change the tube forming die correspondingly.
- Forming Tube Size: φ100mm
- Tube Diameter: 2.5mm
- Generally Forming Length: 210mm
- Pressure: 14Mpa
- Machine Size and Weight: Based on different manufacturers, this data may vary.
Price of Tube Flaring Machine
Tube flaring machines also have different configurations according to different manufacturers and different requests from different customers. Generally, the tube beading machine costs at least USD4000 per set.
The Application of Tube Flaring Machine
- Fuel System: Flares are formed at the ends of fuel lines to ensure leak-free connections for fuel.
- Refrigeration pipes: Form flares at the ends of refrigerant pipes to ensure sealing and connection of refrigerant.
- Condenser and Evaporator Tubing: Flaring is used in these systems to improve the reliability of the connection.
Whether you need 20°, 37°, or 45° flares, or want to customize the flaring angle, contact us to get the solution!
Tapering Machine
Tapering machine is a specific tube end former used to process tubes or bars into a tapered shape. You can use this machine to taper not only round tubes but also square tubes with different materials, such as iron tubes, steel tubes, aluminum tubes, etc.
How the Tapering Machine Works?
- Install the tube tapering die into the machine.
- Start the pipe tapering machine.
- Insert the tube into the rotating mold in the machine.
- Tube forming is done, get the tapered tubing out of the machine and measure the size of the tube, to see if the size meets the customer’s request.
The Main Features of the Tapering Machine
- Tube Forming/Tapering Die: This is the key to taper the tube size and shape, needs to be customized according to the customer’s request.
- Driving System: The hydraulic system supplies the power and the speed reducer controls the speed.
Technical Parameters of Tapering Machine
The tube tapering machine is also highly customizable according to your specific tube size, you can check details with our engineer. Here is the standard parameters of the machine.
- Tapering Tube Size: φ80mm
- Tapering Tube Thickness: 2mm
- Spindle Speed: 177 Rpm
- Power of Motor: 11kw
- Forming Time: 6 to 15 seconds
- Machine Size and Weight: Based on different manufacturers.
Price of Tapering Machine
The same, tapering machine price is also based on your specific needs and our engineer will design the machine accordingly to meet your production needs. Generally, the tube tapering machine will cost at least USD 5,000 per set.
Application of Tapering Machine
- Table and Chair Legs: Tapered tube design increases aesthetics and stability.
- Light Poles and Flagpoles: Tapered design increases strength and reduces wind resistance.
- Engine Components: Certain tapered parts optimize airflow and combustion efficiency.
- Exhaust System: Tapered components for improved airflow.
Pipe Embossing Machine
Here the pipe embossing machine we talk about is another form of tube swaging machine. This swaging machine uses the cold forming technique to form the metal tubes into various shapes.
The rotary swaging machine normally uses 4 pcs of forming die to achieve the precise forming result and ensure the forming consistency for mass production.
How Pipe Embossing Machine Works?
- Choose the forming mold you want to form the tube and install it into the machine.
- Start the machine.
- Feeding the tube into the machine, a few seconds later, your tube has formed.
- Get the tube out of the machine and measure the size and check the shape.
The pipe embossing machine and tapering machine all belong to tube swaging machines, their biggest difference is the different forming molds, and this kind of forming mold can be customized according to your request. Consult with our engineers to customize a tube swaging machine Today!
The Main Features of Pipe Embossing Machine
- Forming Die: Used to form tubes into various shapes.
- Driving System: Generally, use a hydraulic system to drive the machine.
Technical Parameters of Pipe Embossing Machine
- Tube Diameter: 76mm
- Tube Thickness: 2.0mm
- Main Motor: 5.5kw
- Spindle Speed: 200rev/min
- Machine Size and Weight: Based on different manufacturers
Price of Pipe Embossing Machine
The price of embossing machine also depends on what working capacity you purchase. Generally, the cost of pipe embossing machine is at least USD8000 per set.
The Application of Pipe Embossing Machine
- Furniture Manufacturing: Used to make table legs, and bed columns to form a decorative and structural embossed pattern.
- Stair Handrail: Used to make stair handrails to improve aesthetics and anti-slip performance.
- Walking stick: Used to make a walking stick to provide an anti-slip function and decorative effect.
- Metal handle: Formed on the handles of spoons and shovels to improve the grip and aesthetics.
Above are the 7 types of industrial tube end forming machines that are normally used for mass production with high accuracy and high efficiency. Each of them has a different function and forms the tube in different shapes. Do you find the proper tube end formers from above to make the end forming tube? If not, contact our engineer to customize your ideal machine.
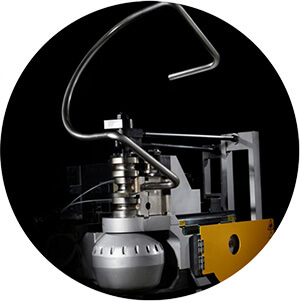
Denis Lau
Denis Lau has 20 years of work experience in the metal processing industry. His major in university was mechanical engineering, and after graduation, he started from the bottom of the workshop, gaining extensive hands-on professional experience and the ability to tackle challenges from various industries.